获取试验方案?获取试验报价?获取试验周期?
注意:因业务调整,暂不接受个人委托测试望见谅。
外形尺寸检测是制造和质量控制中的关键环节,用于确保产品符合设计规格。以下是关于外形尺寸检测的详细指南:
一、常用检测方法
-
手动测量工具
- 工具:卡尺、千分尺、高度规、塞规、环规。
- 适用场景:小批量、简单几何形状或精度要求较低(±0.01mm以上)。
- 优点:成本低、操作灵活。
- 缺点:依赖操作者技能,效率低。
-
光学测量仪
- 技术:投影仪、显微镜、影像测量仪。
- 精度:可达±1μm,适合微小零件(如电子元件)。
- 原理:通过图像分析计算尺寸。
-
三坐标测量机(CMM)
- 精度:亚微米级(0.1-1μm)。
- 功能:测量复杂曲面、孔位、三维尺寸。
- 缺点:速度较慢,设备昂贵。
-
激光扫描/3D扫描
- 技术:结构光、激光三角测量。
- 速度:每秒数百万数据点,适合逆向工程或复杂曲面。
- 输出:3D点云数据,可对比CAD模型。
-
机器视觉系统
- 组成:工业相机、光源、图像处理软件。
- 应用:自动化生产线实时检测(如汽车零部件)。
- 精度:取决于相机分辨率,典型±0.01mm。
二、关键影响因素
-
环境控制
- 温度:ISO标准要求20±1℃(金属件尤其敏感)。
- 振动:需使用防震台,避免外界干扰。
-
设备校准
- 频率:按ISO 9001标准定期校准(如CMM每年一次)。
- 方法:使用标准量块或参考件。
-
被测物处理
- 清洁:去除油污、毛刺。
- 固定:使用夹具避免测量时移动(如V型块固定圆柱体)。
-
材料特性
- 变形控制:软材料(如橡胶)需非接触测量,或使用低测量力探头。
三、检测流程
-
准备阶段
- 确认图纸要求(如GD&T标注)。
- 选择合适设备(如孔径≤5mm优先选光学测量)。
-
定位与固定
-
测量执行
- 手动工具:多次测量取平均值(如3次)。
- 自动化系统:编程设定测量路径(CMM)或扫描区域。
-
数据分析
- 计算CPK/PPK(过程能力指数),判断是否在公差带内(如±0.05mm)。
- 超差处理:触发报警或自动分拣(自动化产线)。
-
报告生成
- 输出格式:PDF/Excel,包含实测值、公差、偏差图。
四、行业应用案例
-
汽车行业
- 检测项:发动机缸体孔径、齿轮齿距。
- 方法:在线激光扫描+SPC实时监控。
-
航空航天
- 案例:涡轮叶片轮廓检测,精度要求±5μm。
- 工具:高精度CMM或蓝光扫描仪。
-
消费电子
- 挑战:手机外壳弧形边缘检测。
- 方案:多相机视觉系统+AI算法补偿反光。
五、选型建议
- 精度需求:
- 低(>0.1mm):手动工具。
- 高(<10μm):CMM或光学测量。
- 批量:
- 小批量:手动/半自动。
- 大批量:集成视觉系统或机器人测量站。
- 预算:
- 低成本:千分尺(50)或二手���(50)或二手CMM(20k起)。
- 高投资:全自动检测线($100k+)。
六、常见问题解决
- 误差偏大:检查环境温度波动或设备校准状态。
- 重复性差:优化夹具设计或改用非接触测量。
- 数据波动:分析测量力影响(如千分尺过紧导致变形)。
通过合理选择方法和严格流程控制,外形尺寸检测可有效提升产品合格率。建议定期进行GR&R(量具重复性与再现性分析)验证检测系统的可靠性。
实验仪器
测试流程
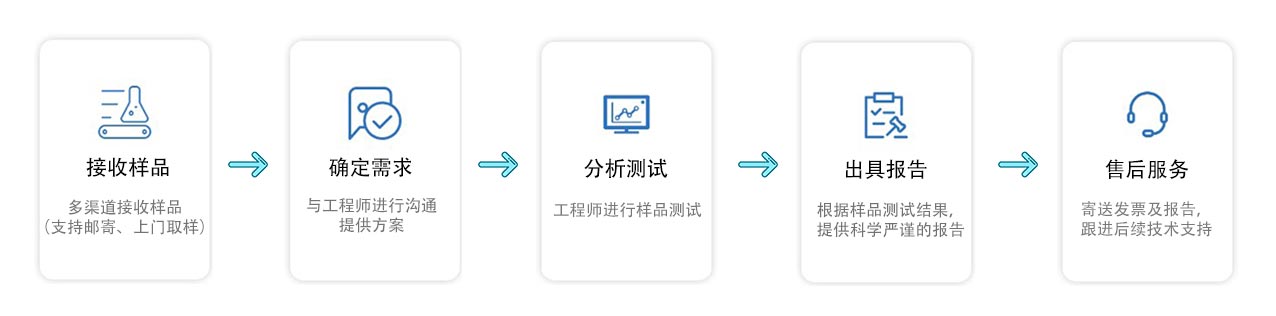
注意事项
1.具体的试验周期以工程师告知的为准。
2.文章中的图片或者标准以及具体的试验方案仅供参考,因为每个样品和项目都有所不同,所以最终以工程师告知的为准。
3.关于(样品量)的需求,最好是先咨询我们的工程师确定,避免不必要的样品损失。
4.加急试验周期一般是五个工作日左右,部分样品有所差异
5.如果对于(外形尺寸检测)还有什么疑问,可以咨询我们的工程师为您一一解答。